Hi everyone,
Well after lots of reading and dreaming I finally put together a DIY solar panel. Ive been facinated about solar since I was a kid, my parents have run their house on solar for almost 30 years. Their failful old BP 40w module still puts out 2 amps after 30 years.
After looking at a few DIY guides, I wasnt too impressed about the plywood designs, whilst they might work I have my doubts about them even lasting 5 years. So after hunting around some more I can across a site in Nicaragua, they use silcone (sylgard) to ecapsulate their cells. Then I found a few videos on youtube also. This looked like a much better way of weather proofing the cells. Also a lot of the earlier panels were made this way, some lasting 30 years plus.
So I orderd some evergreen string cells, and got to work.
However I whilst I orded the sylgard, it took weeks to arrive, in the meantime I was getting bits like glass and frame together in preperation. I came across some dowcorning silcone in the hardware store, it was electrical grade and non corrosive, it also can handle high temperatures and UV etc.
I came up with the idea of laying down the cells on the glass, then simply using the silicone caulk to seal the cells down. I completely sealed the cells with it, it came out $60 cheaper then sylgard (postage is $35). The result is I have the cells totally sealed in a similar silicone to sylgard, there is no worry about the caulk blocking the sunlight as its only on the sides and behind the cells. There are no bubbles infront of the cells either, a common problem with sylgard.
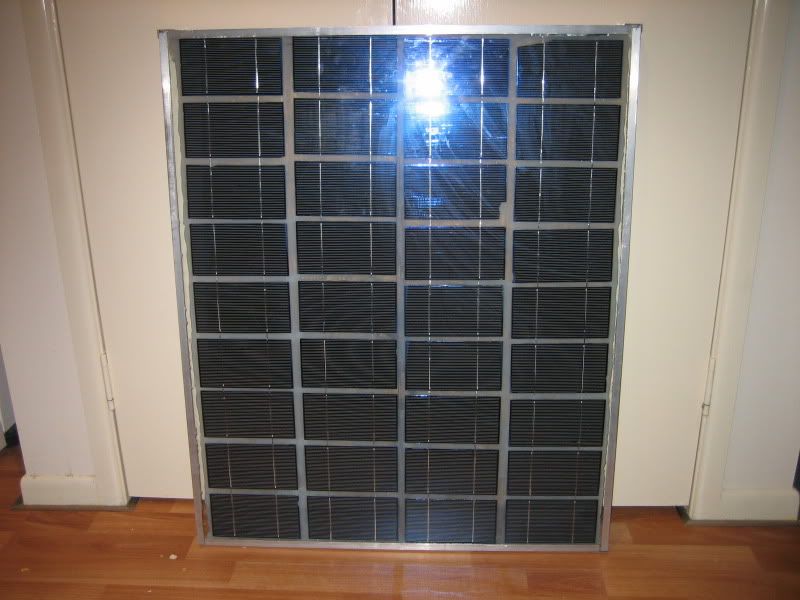
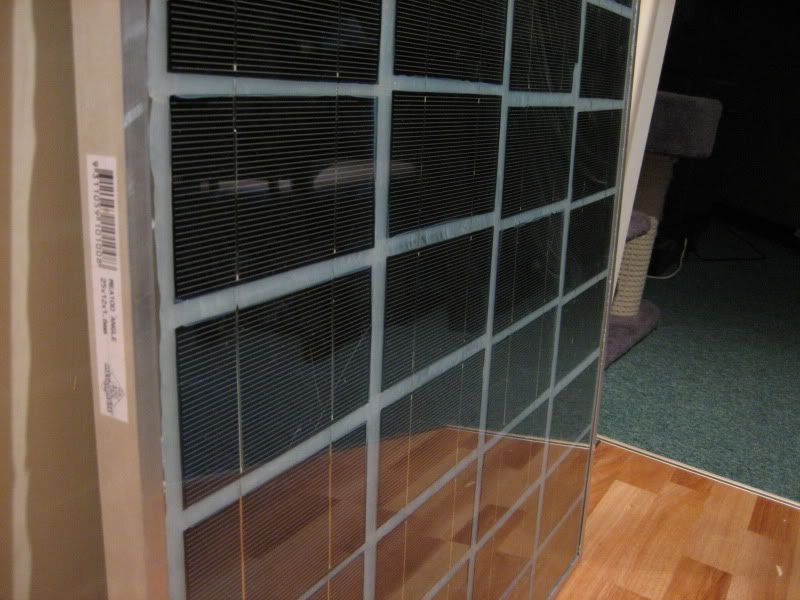
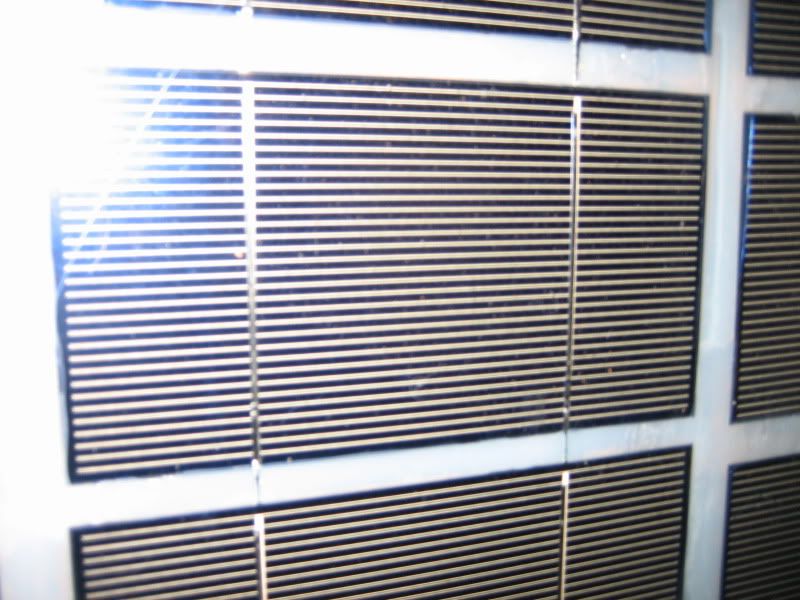
I was very suprised with the results of the panel, its putting out 3.7 amps and 20.5 volts. This drops to about 3.5 and 19 volts in scorching heat, lying flat on the ground also so no ventilation under the panel doesnt help. So its pretty close to a factory built 60w panel.
As you can see like anyone who has never handled solar cells before, i managed to chip some, unfortunately this effects all cells in the panel and drops the amps down a smidgen.
I have left the panel outside for a few weeks, through a storm and rain, minor hail. I even left it on wet grass in the sun for a few days, the back of the panel was soaked, but not one bit of moisture got into the cells. So im happy so far. I have chosen 5mm glass, after speaking to a guy that sold a lot of glass to a caravan park that used 5mm glass for their hotwater panels, he said they have been through heaps of hail storms with no worries.
Ive managed to pick up 5 second hand glass sheets for $3 a sheet 8mm shelving glass, i suspect its tempered, all up Ive worked out I can build the panels for about $140.
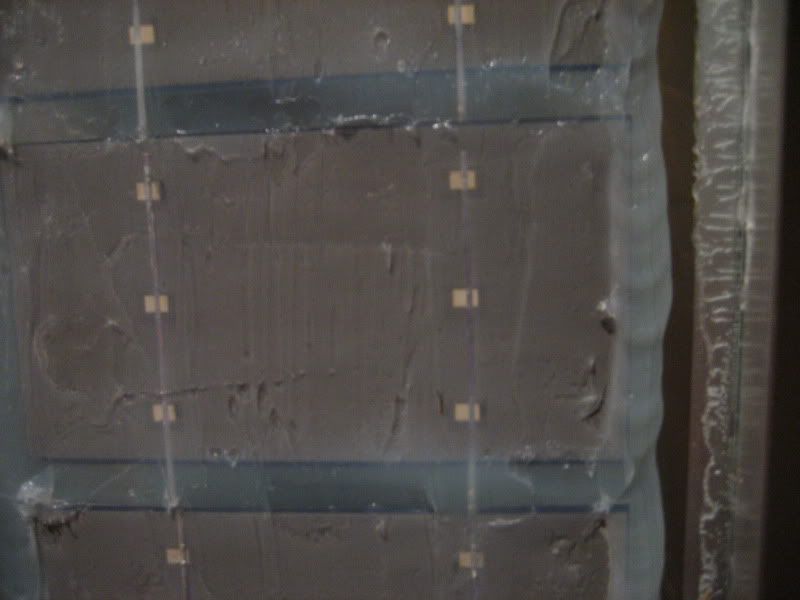
cell sealed with silcone.
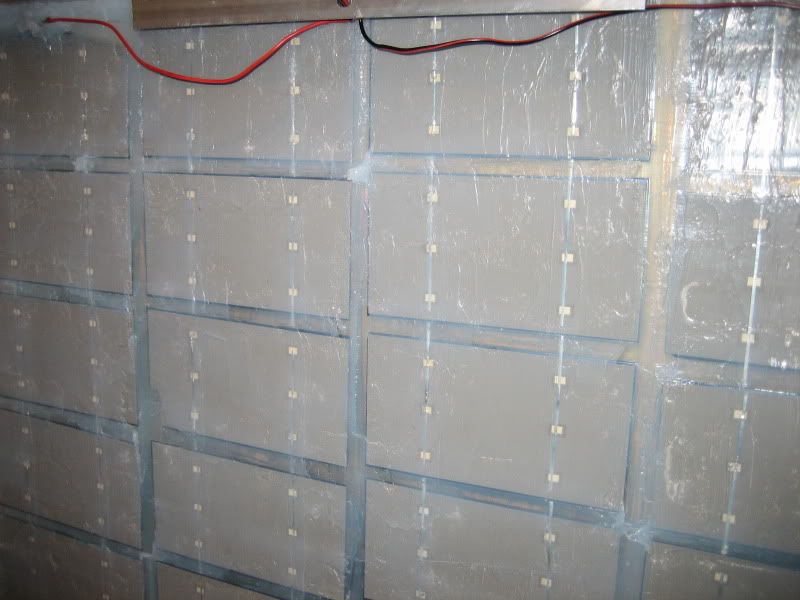
I have plans to use one for camping etc and give the rest to my parents for now, they are cheap to make, and Ill be keen to see how they last over time, most of all I get a buzz outta of it !!
being my first panel, it took a lot longer then I thought, next one should be easier.
Im also looking into sealing the cells, then laying down a plastic cover sheet on the back of the cells, this will reduce the need for so much silcone and reduce time and costs. Its just an idea at this stage.
Well after lots of reading and dreaming I finally put together a DIY solar panel. Ive been facinated about solar since I was a kid, my parents have run their house on solar for almost 30 years. Their failful old BP 40w module still puts out 2 amps after 30 years.
After looking at a few DIY guides, I wasnt too impressed about the plywood designs, whilst they might work I have my doubts about them even lasting 5 years. So after hunting around some more I can across a site in Nicaragua, they use silcone (sylgard) to ecapsulate their cells. Then I found a few videos on youtube also. This looked like a much better way of weather proofing the cells. Also a lot of the earlier panels were made this way, some lasting 30 years plus.
So I orderd some evergreen string cells, and got to work.
However I whilst I orded the sylgard, it took weeks to arrive, in the meantime I was getting bits like glass and frame together in preperation. I came across some dowcorning silcone in the hardware store, it was electrical grade and non corrosive, it also can handle high temperatures and UV etc.
I came up with the idea of laying down the cells on the glass, then simply using the silicone caulk to seal the cells down. I completely sealed the cells with it, it came out $60 cheaper then sylgard (postage is $35). The result is I have the cells totally sealed in a similar silicone to sylgard, there is no worry about the caulk blocking the sunlight as its only on the sides and behind the cells. There are no bubbles infront of the cells either, a common problem with sylgard.
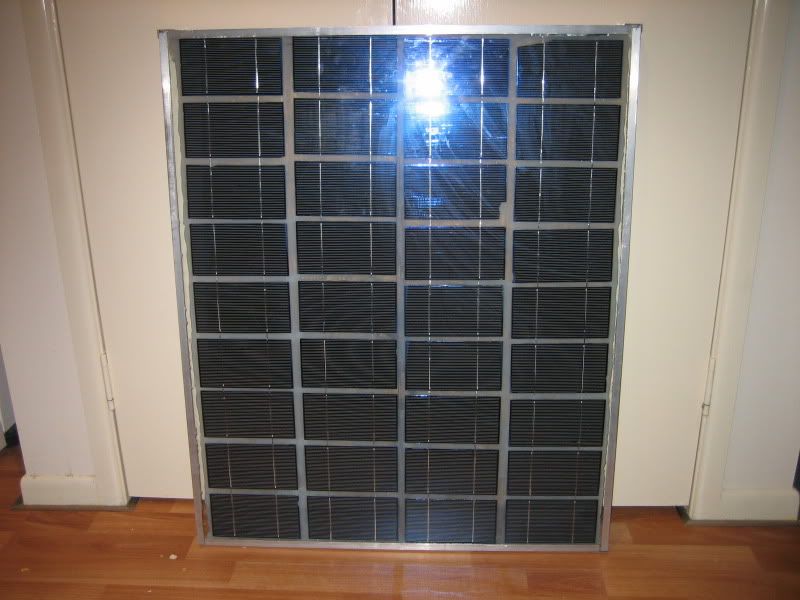
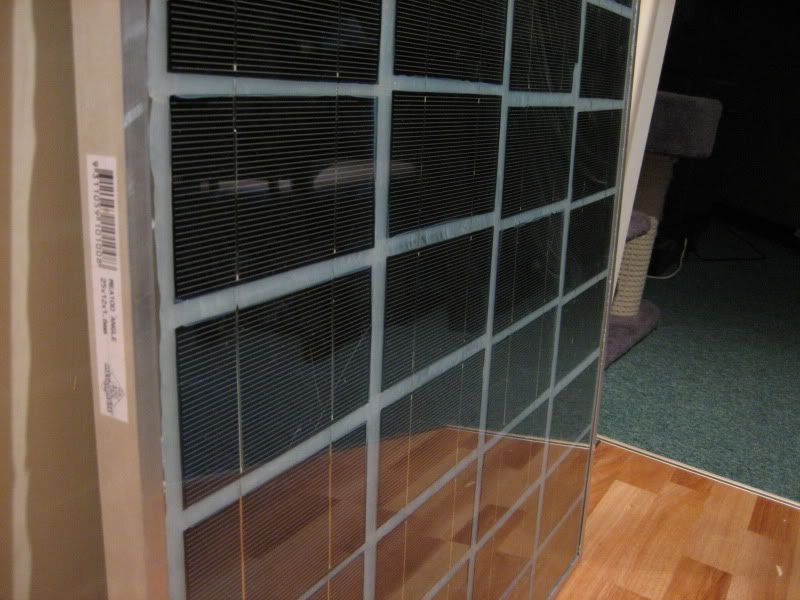
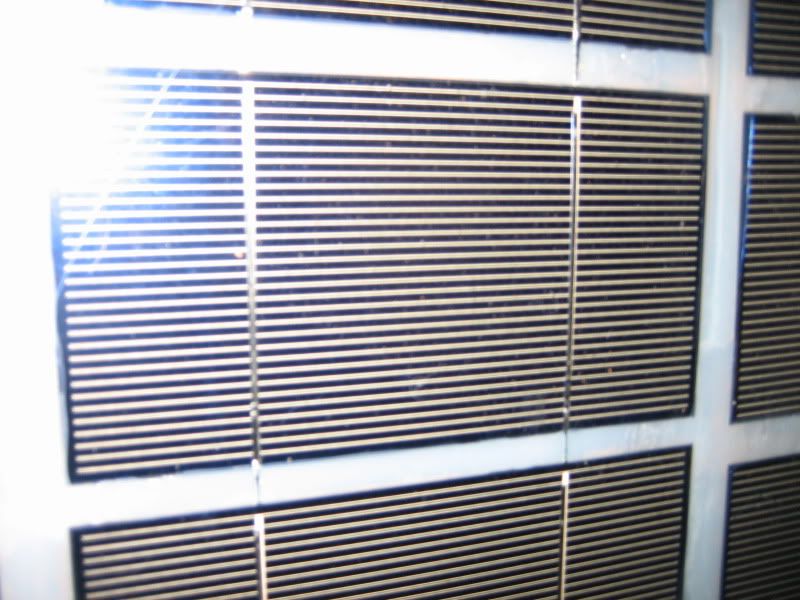
I was very suprised with the results of the panel, its putting out 3.7 amps and 20.5 volts. This drops to about 3.5 and 19 volts in scorching heat, lying flat on the ground also so no ventilation under the panel doesnt help. So its pretty close to a factory built 60w panel.
As you can see like anyone who has never handled solar cells before, i managed to chip some, unfortunately this effects all cells in the panel and drops the amps down a smidgen.
I have left the panel outside for a few weeks, through a storm and rain, minor hail. I even left it on wet grass in the sun for a few days, the back of the panel was soaked, but not one bit of moisture got into the cells. So im happy so far. I have chosen 5mm glass, after speaking to a guy that sold a lot of glass to a caravan park that used 5mm glass for their hotwater panels, he said they have been through heaps of hail storms with no worries.
Ive managed to pick up 5 second hand glass sheets for $3 a sheet 8mm shelving glass, i suspect its tempered, all up Ive worked out I can build the panels for about $140.
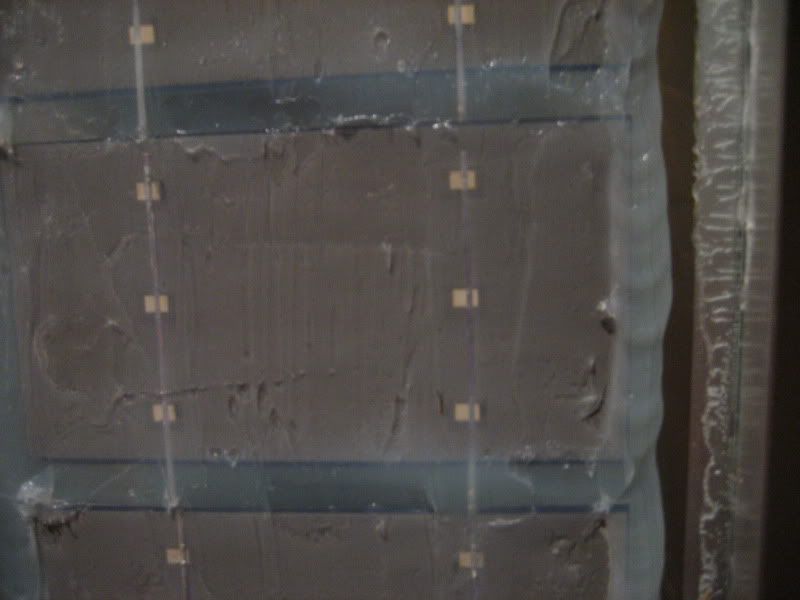
cell sealed with silcone.
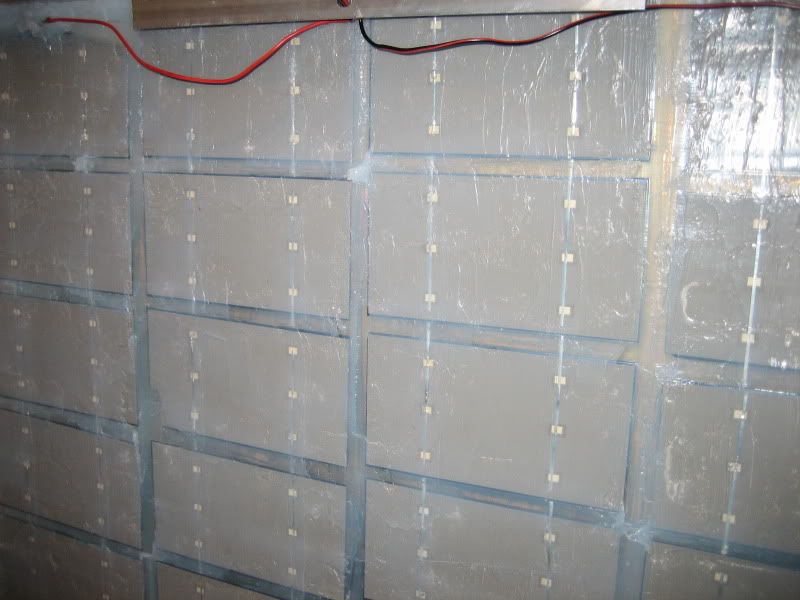
I have plans to use one for camping etc and give the rest to my parents for now, they are cheap to make, and Ill be keen to see how they last over time, most of all I get a buzz outta of it !!
being my first panel, it took a lot longer then I thought, next one should be easier.
Im also looking into sealing the cells, then laying down a plastic cover sheet on the back of the cells, this will reduce the need for so much silcone and reduce time and costs. Its just an idea at this stage.
Comment